|
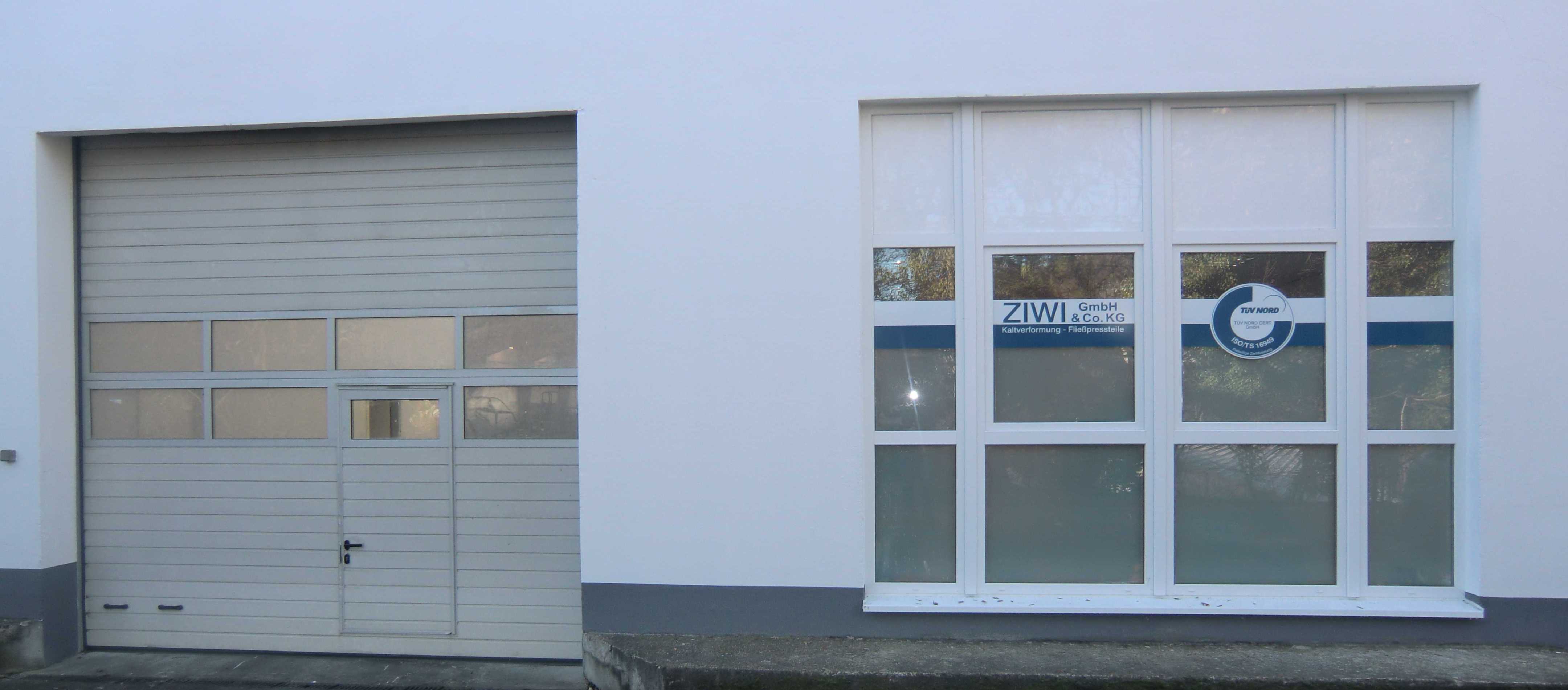
Kierspe: the Manufacturing plant III
ZIWI -
Kaltverformung - Fließpressteile
Ziegeweid & Winkelmeyer GmbH & Co. KGFriedrich-Ebert- Str. 275
D - 58566 Kierspe
In the "ZIWI" Ziegeweid & Winkelmeyer GmbH & Co.KG Kierspe - Werk 3, the activities are limited exclusively to the production of metallic mass cold forming / flow molding
parts.
In order to meet the increased demand for extruded parts, in 2006 we took over ZIWI Cold Forming and Extrusion Parts in Lüdenscheid.
Since we rely here on the experienced specialists and the high-quality technical equipment of the company, we can offer customers since then the advantages of cold forming at a high level. At the location designated by us as Plant III, we mainly produce extruded parts made of wire diameters from 2.9 to 16 mm.
After the acquisition, we invested in multi-stage technology in particular.
This enables us to produce complex, high-quality extruded parts for our customers. In addition, we have high-performance machines for machining and machining in Kierspe that can not be realized by the pressing process itself.
To ensure that your orders are completed in the shortest possible time, we also have our own department for toolmaking.
Of course, we would be happy to advise you on the most appropriate method for the parts you need and the specific purpose of the
application.
Technology
In Kierspe we use multi-stage cold forming presses, e.g. the manufacturer
-
Hilgeland
-
Nakashimada
-
Peltzer & Ehlers
-
Sacma
-
National Kayser
and further manufacturing.
In the forming technique, the cold massive forming is realized by means of pressure molding, in which the part to be produced is not heated, but is deformed in the cold state in presses between the ram and a die by means of enormous pressures. Due to the corresponding shapes of dies and dies, the material is forced to flow through the free spaces defined by die and die. In this case also diameter graduations (reductions or full forward flow pressings) are
realized.
If the workpiece is reduced, the workpiece is extended in each case in a reduced diameter. If an intermediate space, in which the material enters during pressing, is formed between the die inside and the punch, a corresponding cavity is formed in the part. This process is referred to as a cup, in which forms by the penetration of the punch in the starting workpiece, a "hole". Depending on the flow direction of the material during pressing is spoken by the forward or reverse
extrusion.
|
|
Schematic sequence of the cold forming of a step mandrel
|
|
|
|
|
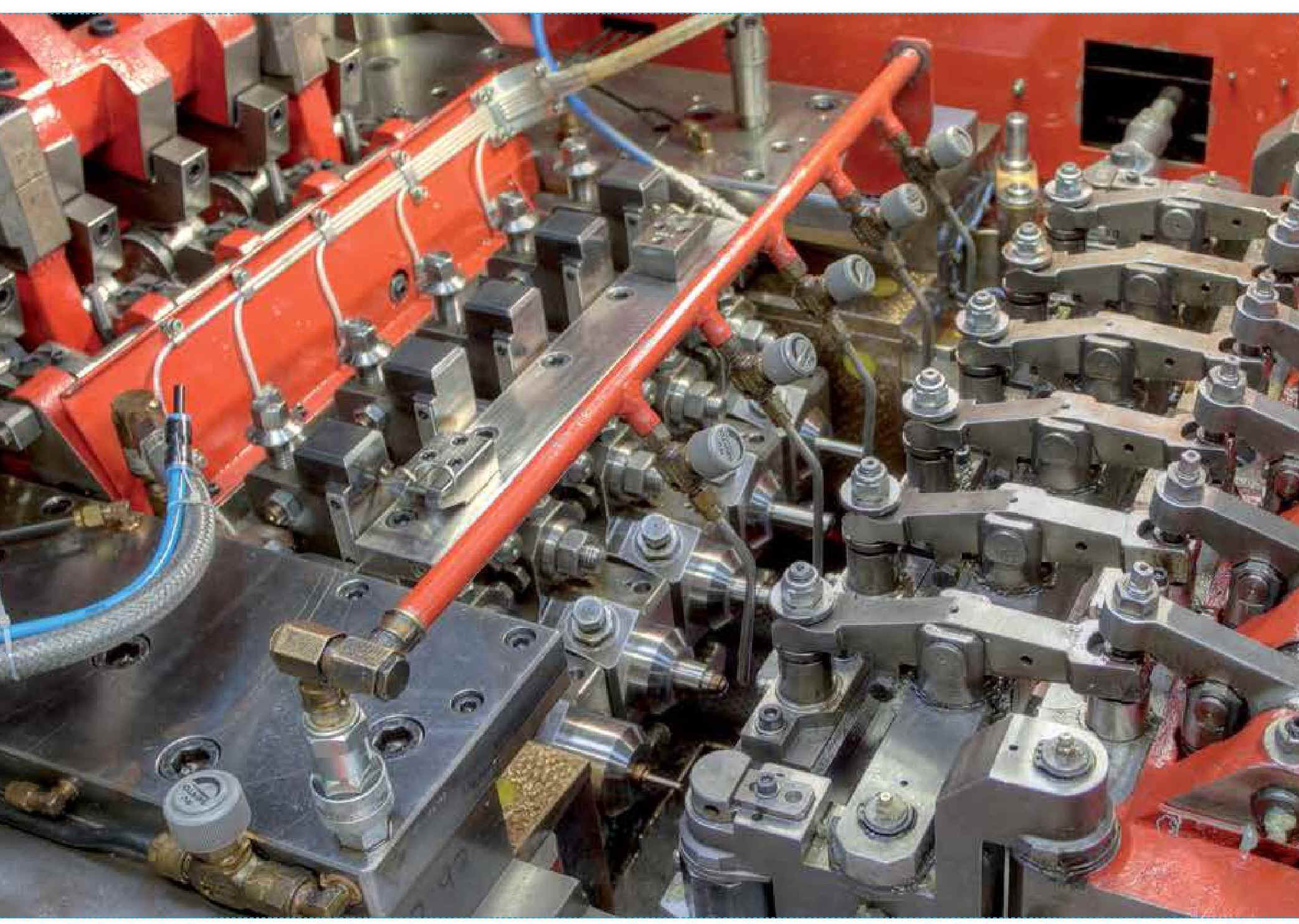
Inside view of a cold forming press type Sacma SP360 - 5S
|
|
|
Cold forming or turned part?
For the production of mass-produced items such as screws, sleeves, axles, bolts and stepped moldings, the use of cold forging is particularly suitable. Compared to machining, the material used is almost completely converted into articles. Thus, with increasing material weight and price, in addition to the significantly faster cycle time, the achievable savings in material compared to metal-cutting production are gaining in
importance.
Subsequent compensation can be avoided to the extent that the resulting work hardening (targeted at certain points), not least by the homogeneous material and the favorable fiber flow during cold extrusion, high values for tensile, bending - and torsionsbeanspruchte parts can be achieved.
Further advantages of cold extrusion are a smooth surface with roughness similar to a ground surface and good dimensional
accuracy.
In addition, the high achievable production piece count per minute is cost-reducing compared to the production of a turned part.
Because of these reasons, the method of cold forming is already paying more attention to the design already today. The cost advantage over machining becomes interesting for our customers, above all in large series. The tool development and tool production costs, which are not insignificant compared to the machining, can be amortized after a short time via the savings potential of better material use and the higher production per minute.
|
|
|
|
|
|
Outlook: new location Kierspe
Of course, we would like to be able to offer our customers all important services in first-class quality and in the shortest possible time. Especially in cold forming and extrusion we want to expand and expand our offer.
The required production and production areas are designed by the customer requirements for process and product quality with corresponding potential for further growth. In 2013, Plant III was relocated to new premises in Kierspe for better planning and control of operations and processes..
|
|